Glass 101: Fused Silica vs. Quartz
Posted Jul 27, 2021
on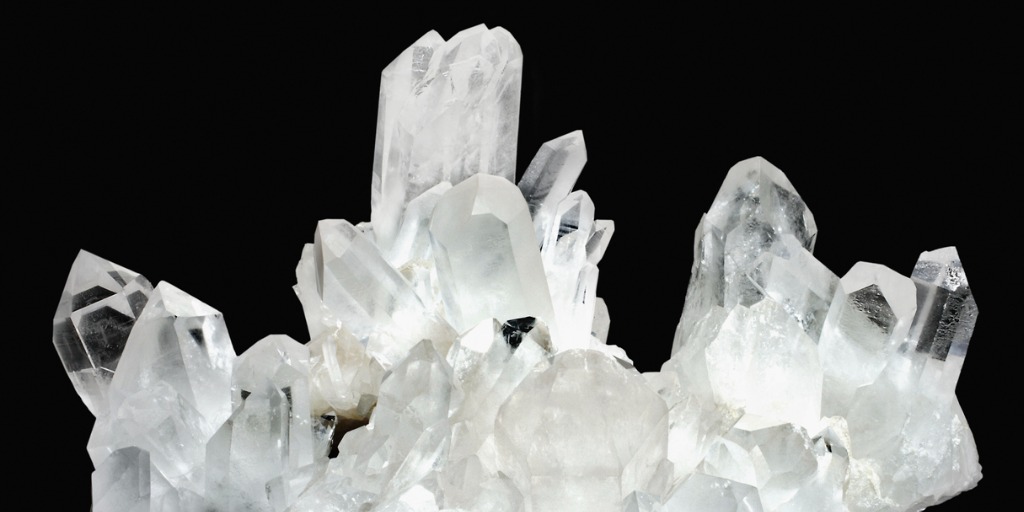
Quartz, fused quartz, quartz glass, silica, fused silica… the list of terms used to describe various silica-based materials is long, confusing, and often misunderstood. In this article, we take a close look at the unique properties of quartz and fused silica (and a few related materials), and clear up the confusion surrounding these terms.
Quartz vs. Silica
The first important thing to know about quartz and fused silica is that they both primarily consist of the same ingredient: silica, also known as silicon dioxide. Silica has the chemical formula SiO2 and is the primary constituent of most types of glass. The main form in which silica is found in nature is the mineral quartz: a hard, transparent crystalline material that makes up an appreciable fraction of the Earth’s crust. While quartz primarily consists of silica, it also contains naturally occurring impurities in various proportions depending on its geological origin.
So, silica is a specific chemical compound, silicon dioxide, with the chemical formula SiO2. On the other hand, quartz is a naturally occurring crystalline mineral, which consists primarily of silica but contains some impurities.
Crystalline and Amorphous Solids
To fully understand the differences between different silica-based materials, we first need to review the fundamental differences between crystalline solids and amorphous solids.
The distinction comes down to how atoms are arranged inside the solids. In a crystalline solid, the constituent atoms are arranged in regular, repeating patterns known as crystal lattices. Quartz is an example of a crystalline silica-based material: silicon and oxygen atoms are arranged in a well-defined ordered structure.
However, in an amorphous solid, the atoms have no long-range order. The seemingly random arrangement of molecules in an amorphous solid resembles that of a liquid, except that they are fixed in place and don’t move around. Most materials that we think of as “glass” are amorphous solids: in fact, any material with an amorphous atomic structure can be described as “glassy”.
Whether atoms are arranged in an orderly manner or oriented randomly can profoundly influence a material’s characteristics. One of the most striking examples is the glass transition effect exhibited by amorphous solids. Outside the world of silica or other oxide-based materials, disordered “glassy” metals are often used for their unusual mechanical characteristics compared to conventional metals.1
Silica-based materials – like quartz – can be characterized both in terms of their chemical composition and whether they are crystalline or amorphous.
Defining Silica-Based Materials
Now that we’ve reviewed some important fundamentals, we can define the differences between quartz, fused silica, and other silica-based materials.
Quartz
As mentioned previously, quartz is the main form in which silica occurs in nature. Quartz is a crystalline solid; so, while it can resemble glass both in terms of its appearance and its chemical makeup, it has very distinct properties from glass.
Industrial applications of quartz (that is, the crystalline mineral) are limited, but include quartz crystal oscillators in electronic systems – most familiarly in wristwatches.
Perhaps confusingly, “synthetic quartz” can be manufactured for industrial quartz applications. This would perhaps be better referred to as crystalline silica, but is often referred to simply as “quartz.”
Fused Silica and Fused Quartz
Here, the word “fused” refers to a processing step: fused silica is nominally pure silica that has been melted and cooled to form a glassy, amorphous solid. Fused silica resembles other glasses in many ways; but it does not contain any additives. Fused silica is a specialty material with a number of high-performance applications.
The terms “fused silica” and “fused quartz” are often used interchangeably. More accurately, “fused quartz” refers to an amorphous solid formed by melting naturally-occurring quartz. So, while fused silica is ostensibly pure SiO2, fused quartz contains impurities depending on the quartz that was used.
Silica Glass and Quartz Glass
These terms are typically used in a more generic sense, and can usually be considered interchangeable. Both of these terms could refer either to fused silica or fused quartz.
Applications of Fused Silica
While fused silica is chemically similar to quartz, its amorphous structure gives it a number of distinct and highly desirable thermal, mechanical and electrical properties.
Glasses commonly contain additives such as alkali, alkaline earth, or other oxides to lower the glass processing (melting) temperature and to improve chemical and physical properties – but fused silica is very pure. Consequently, it has higher working temperatures but offers different characteristics from other glasses.
Fused silica has a very low coefficient of thermal expansion, meaning it does not expand or contract much when heated or cooled. As a result, fused silica is highly resistant to thermal shock and can withstand very rapid heating or cooling without cracking. The thermal characteristics of fused silica make it highly valuable for high-temperature industrial components such as crucibles, trays, and boats for steelmaking and glass manufacture.2
Fused silica is transparent to a very wide spectrum of light, extending from deep ultraviolet to far-infrared. This makes it a key component in optical fibers, as well as in a range of lenses, mirrors, and other UV- or IR-transmitting optics.3,4
Fused silica is also extremely chemically inert and resistant to most acids (with the notable exception of hydrofluoric acid). This chemical inertness lends fused silica to biomedical applications, often taking the form of porous silica.
The combination of thermal stability, transparency, and strength makes fused silica a strong candidate for new and developing applications such as photolithography substrates, etched microwave circuits, and as a protective layer in semiconductor devices.
Custom Glass Solutions from Mo-Sci
Mo-Sci develops and manufactures a range of high-performance glasses for technical applications. To find out more about our fused silica and porous silica products, or to discuss a custom glass application, get in touch with a member of our team today.
References and Further Reading
- Glassy metal set to rival steel : Nature News. https://www.nature.com/news/2011/110109/full/news.2011.4.html.
- Vert, T. Refractory Material Selection for Steelmaking. (John Wiley & Sons, 2016).
- Khalaf, A. L., Shabaneh, A. A. A. & Yaacob, M. H. Carbon Nanotubes and Graphene Oxide Applications in Optochemical Sensors. in Synthesis, Technology and Applications of Carbon Nanomaterials 223–246 (Elsevier, 2019). doi:10.1016/B978-0-12-815757-2.00010-3.
- Wang, S., Zhou, C., Zhang, Y. & Ru, H. Deep-etched high-density fused-silica transmission gratings with high efficiency at a wavelength of 1550 nm. Appl. Opt. 45, 2567 (2006).