Although the glass is normally only three millimetres thick, there is some possibility of a refraction of the light if you look from the side of the cutter. As described elsewhere, you should be holding your cutter upright in the left to right plane and angled slightly back toward you so that you can look with your dominant eye along the barrel of the cutter and head. This ensures you are directly above the cut line and do not have any refraction caused by the glass.
Friday, 7 February 2025
Cutting from Cartoon
Although the glass is normally only three millimetres thick, there is some possibility of a refraction of the light if you look from the side of the cutter. As described elsewhere, you should be holding your cutter upright in the left to right plane and angled slightly back toward you so that you can look with your dominant eye along the barrel of the cutter and head. This ensures you are directly above the cut line and do not have any refraction caused by the glass.
Wednesday, 24 August 2022
Accuracy in Following the Cartoon
A question arose on Facebook
that resolved itself around the need (or not) to accurately follow the cartoon.
The question itself was whether a pictured piece should be re-cut. It was a
relatively complicated piece, which in its current state left two significant
gaps between the glass and the cartoon line.
The vast majority of responses, was along the lines of don’t worry, just adjust the neighbouring pieces to fill the gaps. (“enjoy yourself” was another theme).
To follow the majority view - make adjustments in other pieces to allow the problem piece to fit - encourages bodge. It does not encourage development in the skills of the craft. It does not encourage long term enjoyment. It pushes improvement well into the future.
The cartoon is the design in line form. Its purpose is to control the construction of the piece. It is important to follow the cartoon to express the design. This means striving to cut and fit the glass to the cartoon as accurately as possible. Line is important in stained glass, as everyone knows. If the glass is not fitted accurately, the lines will not flow according the cartoon and the design.
This is not to say the cartoon cannot be modified. It is important to look at the cartoon in detail once you have been attracted by a design. You need to look at each piece and determine its difficulty. Can I cut it? Is the design overly complicated? How might I modify the cartoon to make easier to cut pieces, and still maintain the overall design? Ensure the cartoon is drawn with accurately thin lines for the form of the craft – copper foil or leaded glass, and fused glass. Revise your cartoon to respond to the answers to this review of it.
Whatever method you use to score and break your glass, fit the piece to the cartoon as accurately as possible to avoid excess work later. The grinder is there to make fine adjustments to the cut piece so it will fit the cartoon. If the glass fits snugly within the cartoon lines, there should be little, or no, alteration required to the cartoon during the rest of the construction.
This is not about the methods you use during the construction of a piece. That is open to many approaches to achieve the same end. It is about an approach to the craft. In particular, it is about how the cartoon is used to guide the work. If the detail of the cartoon is optional, the final result may vary from the original conception significantly.
Craft development is
about striving to perform the actions as accurately as possible throughout the
work. The increased skill level that this develops, provides long-term
enjoyment. And each completed piece will
give a feeling of accomplishment.
Wednesday, 2 March 2022
Accurate cutting
- · You need clean flat surfaces with only a little flexibility, with no glass shards, bumps or warps that would make scoring the glass more difficult.
- · You need to work at a comfortable height – usually about 10cm below your elbow.
- · You should be moving your torso and sometimes your whole body to score, following the cutline.
- · Your elbow should be at your side and your wrist should be fixed.
- · You need to work at a corner of the workbench to be able to move your body around as you follow a curve.
- · Your cutter should be at right angles to the glass (side to side)
- · The cutter should be angled back toward you slightly, so you can see down the barrel to the scoring wheel. Also, so any unevenness in the glass will not cause the cutter to stall.
- · The pressure should consistently be about 2.5kg or 7 pounds. Do not listen for the sound, as it varies between opalescent and transparent glasses. Heavy pressure on any glass causes unwanted break outs. Score to the pressure, not the sound.
- · Keep a consistent speed. Variability in speed also translates to uneven pressure. Even when you could go fast in scoring, keep to a steady pace.
- · Score and then break each line before going on to the next. Do not score all around the piece in one go. It does not allow for any adjustment, if the cut is not accurate.
Oil filled cutter in classic hold |
- · My preference is to score the glass directly over the cartoon. This involves no extra pattern making.
- · Drawing the lines from the cartoon on top of the glass and then moving the glass to a separate cutting surface is the preference of many.
- · Making pattern pieces with the space for the foil and tolerance already cut out is a preference of many copper foilers.
- · Manipulation of the glass to follow the line exactly.
- · Permanency of the guiding lines drawn onto the glass.
- · Accuracy of the drawn lines.
- · Accuracy of the pattern pieces.
- · Allowing the machine to cut rather than forcing the glass into the blade.
- · Maintenance of the machine.
- · Maintenance of the blade or wire.
Wednesday, 9 February 2022
Fitting Glass in Leading
Wednesday, 29 August 2018
What Cartoon Lines Represent
Wednesday, 4 July 2018
Grinding to Fit
Saturday, 11 March 2017
Drawing an Oval
- Set out the long axis horizontally.
- Set out the short axis at the half way point of the long axis at right angles to the horizontal.
- Measure half the short axis on each side of the long, horizontal axis.
- Calculate half the measurement of the longest line. In this example the long line is 340mm and the short axis is 200mm long.
- Half the long axis is 170mm.
- Use that as a diagonal measurement from the end of the vertical axis.
- Measuring from the end of the shortest line, mark off this amount on the longest line, right and left. You can use a ruler or compass set to the correct length, both will work.
- Insert a pin at both these points.
- Place a piece of thread, string - or in this case a quick release tie - round one pin. Tie a knot in the thread at the far end of the longest line.
- Put a pencil inside the loop. Pull the thread taut and begin to draw the oval. Keep the tension even throughout the drawing to avoid a lopsided oval.
This is a simple method that does not require much in the way of tools, but its accuracy is a result of the degree of attention to details.
Wednesday, 14 September 2016
Line Widths for Cartoons
Thursday, 15 August 2013
Assembling Foiled Pieces
Wednesday, 15 February 2012
Pounce Wheel
![]() |
Two Pounce Wheels of Different Sizes |
![]() |
A crude pounced design |
Tuesday, 10 January 2012
Light Box
Additional notes:
Light box requirements
Flexibility
Top surfaces
Lighting
Thursday, 5 January 2012
Paper
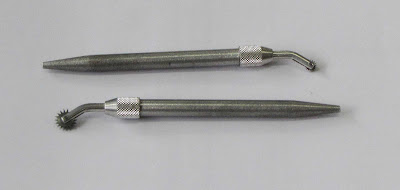
Monday, 5 December 2011
Reworking Designs
- Cropping the design can transform it. The focus of the design can be enhanced by removing some of the surrounding “information”. The change of proportions say from landscape to portrait can make significant differences.
- Enlarging and using only a portion of the original design can be a solution. This is similar to the cropping operation, but has the added advantage of making the pieces larger and easier to cut.
- Further simplification of background design lines can be considered. This will bring the focus back onto the main part of the image.
- Changing relative proportions can transform the design, e.g., by enlarging a busy background, it can be made simpler and easier to read the whole panel.
Wednesday, 30 November 2011
Design Sources
- draw lead lines on an illustration to make it suitable for stained glass, using the fewest lines possible
- Use your photographs of interesting subjects and scenes
- Study abstract representations. Dissect – decomposition is a popular word - and analyse how the work is put together.
- Use geometric design as an introduction to abstract design. This forces your attention to structure, balance and colour.
- Once the distribution of the physical and visual weights is understood, this enables the jump to more free forms of abstraction.
Friday, 25 November 2011
Beautiful Design Lines
- Put the work aside for a day or two before taking it out and looking at it again.
- Alternatively, pin up the design on a wall where you can look at as you pass by. When you see a change to be made, do it immediately and pin it back up.
- Get a new perspective, e.g.:
- Turn it upside down. This will enable you to observe differences and spot inconsistencies
- Look at it in a mirror. You might see people studying still life or live subjects together with their drawing in a hand mirror to get a new perspective that will help spot difficulties.
- Put the design on the floor and climb a ladder to look at it. This provides distance and changes the angle at which you look at your design.